New technology 3D prints glass microstructures with rays of light
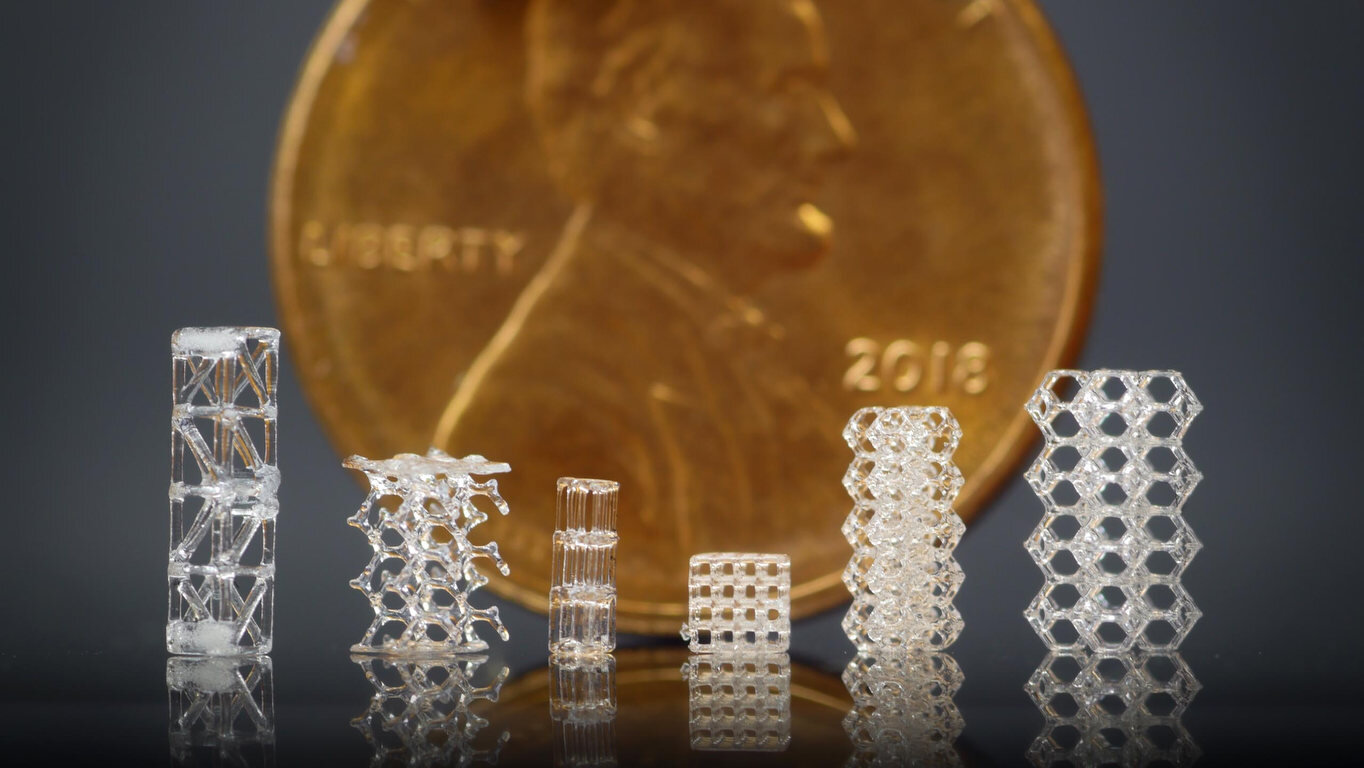
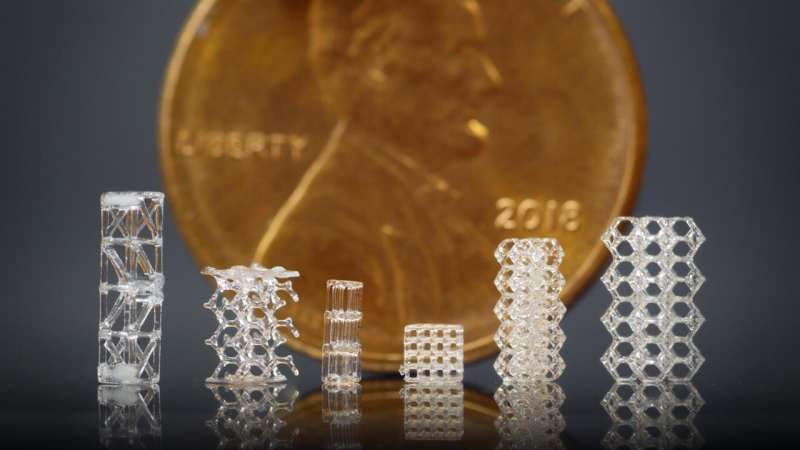
Scientists at UC Berkeley have created a new way to 3D-print glass microstructures that is more quickly and provides objects with larger optical excellent, style overall flexibility and energy, in accordance to a new review revealed in the April 15 challenge of Science.
Performing with scientists from the Albert Ludwig University of Freiburg, Germany, the scientists expanded the capabilities of a 3D-printing course of action they designed a few several years ago—computed axial lithography (CAL)—to print a lot finer options and to print in glass. They dubbed this new process “micro-CAL.”
Glass is the most popular material for developing elaborate microscopic objects, together with lenses in compact, higher-quality cameras utilized in smartphones and endoscopes, as well as microfluidic devices utilized to analyze or course of action moment amounts of liquid. But current production solutions can be slow, high-priced and limited in their ability to satisfy industry’s raising calls for.
The CAL course of action is fundamentally distinct from today’s industrial 3D-printing manufacturing procedures, which establish up objects from slender levels of product. This system can be time-intense and end result in rough surface area texture. CAL, on the other hand, 3D-prints the total item simultaneously. Researchers use a laser to venture patterns of mild into a rotating quantity of light-delicate material, constructing up a 3D light dose that then solidifies in the ideal shape. The layer-much less mother nature of the CAL system allows smooth surfaces and complicated geometries.
This examine pushes the boundaries of CAL to display its capability to print microscale features in glass constructions. “When we very first published this system in 2019, CAL could print objects into polymers with functions down to about a 3rd of a millimeter in size,” claimed Hayden Taylor, principal investigator and professor of mechanical engineering at UC Berkeley. “Now, with micro-CAL, we can print objects in polymers with options down to about 20 millionths of a meter, or about a quarter of a human hair’s breadth. And for the very first time, we have proven how this strategy can print not only into polymers but also into glass, with functions down to about 50 millionths of a meter.”
To print the glass, Taylor and his exploration workforce collaborated with experts from the Albert Ludwig College of Freiburg, who have made a particular resin material that contains nanoparticles of glass surrounded by a light-delicate binder liquid. Digital gentle projections from the printer solidify the binder, then the scientists heat the printed item to clear away the binder and fuse the particles collectively into a good item of pure glass.
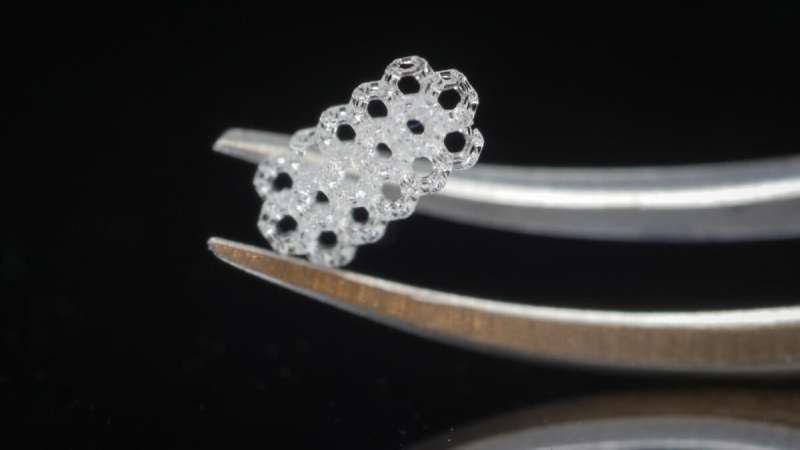
“The crucial enabler below is that the binder has a refractive index that is virtually equivalent to that of the glass, so that gentle passes via the material with virtually no scattering,” reported Taylor. “The CAL printing method and this Glassomer [GmbH]-created product are a fantastic match for every other.”
The exploration crew, which included guide creator Joseph Toombs, a Ph.D. scholar in Taylor’s lab, also ran tests and found that the CAL-printed glass objects had additional consistent strength than these manufactured utilizing a conventional layer-based printing process. “Glass objects are inclined to split more effortlessly when they include much more flaws or cracks, or have a tough floor,” mentioned Taylor. “CAL’s means to make objects with smoother surfaces than other, layer-based 3D-printing processes is for that reason a major likely advantage.”
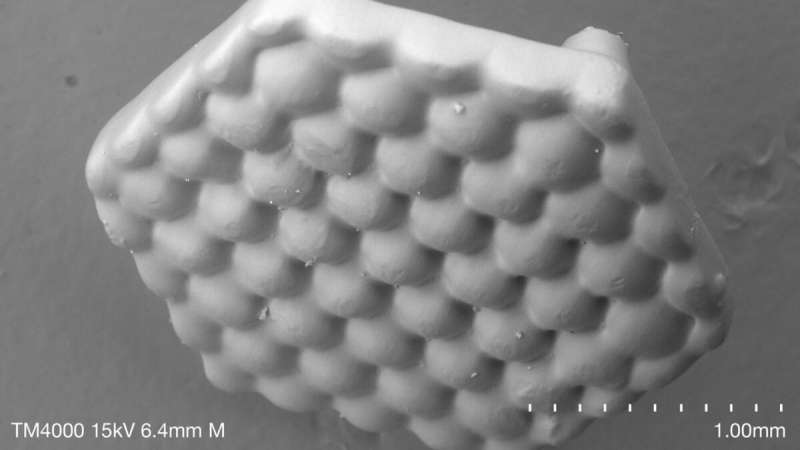
The CAL 3D-printing system presents producers of microscopic glass objects a new and more economical way to fulfill customers’ demanding requirements for geometry, sizing and optical and mechanical attributes. Particularly, this features makers of microscopic optical elements, which are a essential aspect of compact cameras, virtual reality headsets, highly developed microscopes and other scientific instruments. “Becoming equipped to make these components speedier and with extra geometric independence could probably guide to new gadget functions or reduced-charge products,” explained Taylor.
Joseph T. Toombs et al, Volumetric additive manufacturing of silica glass with microscale computed axial lithography, Science (2022). DOI: 10.1126/science.abm6459
Quotation:
New technological innovation 3D prints glass microstructures with rays of mild (2022, April 15)
retrieved 17 April 2022
from https://techxplore.com/information/2022-04-engineering-3d-glass-microstructures-rays.html
This document is topic to copyright. Aside from any good dealing for the reason of personal review or exploration, no
aspect may possibly be reproduced with out the penned authorization. The material is supplied for details applications only.